
Corrosion in the Energy Industry: Understanding the Root Causes and Mitigating Strategies
Corrosion is a major problem in the energy industry, causing high costs in the form of maintenance, equipment downtime, asset replacement, and lost production. Globally, the cost of corrosion is estimated to be $2.5 trillion annually, and this doesn't even take into account employee safety and environmental costs. For example, corrosion under insulation alone accounts for approximately half of the pipe maintenance budget.
Many experts in the industry are knowledgeable about the various mechanisms of corrosion and the complex techniques used to mitigate it. However, by not understanding and focusing on the root causes, the problem of corrosion can become more complicated than it needs to be.
When discussing the intricate details and complications of corrosion, it can be overwhelming and confusing for those not familiar with the terminology. For example: corrosion cells, stress corrosion cracking, intergranular corrosion, Galvanic corrosion, crevice corrosion, filiform corrosion, fretting corrosion, cavitation corrosion, cathodic protection, anodic protection, mill scale, concentration cells, yellow, brown, and black rust, blast profile, and painting “conditions” are all terms used to describe different aspects of corrosion.
However, by understanding the root causes of corrosion and implementing the appropriate mitigating strategies, we can effectively combat this costly problem. Cathodic protection and anodic protection, for example, are methods used to prevent corrosion by controlling the electrical potential of metal surfaces. Mill scale, a thin layer of iron oxide that forms on the surface of hot-rolled steel, can also play a role in corrosion and should be removed before painting or coating.
It is important to note that different types of corrosion require different methods of mitigation. For example, galvanic corrosion occurs when two different metals are in contact with each other in an electrolyte, while crevice corrosion occurs in confined spaces where the flow of electrolyte is restricted. Stress corrosion cracking, on the other hand, occurs when a combination of stress and a specific environment, such as a particular pH or temperature, causes cracking in a metal.
Understanding the root causes and appropriate mitigating strategies for corrosion is essential for effectively combatting this costly problem in the energy industry. By taking the time to understand and address the underlying issues, we can reduce the impact of corrosion on equipment, production, and overall industry costs.
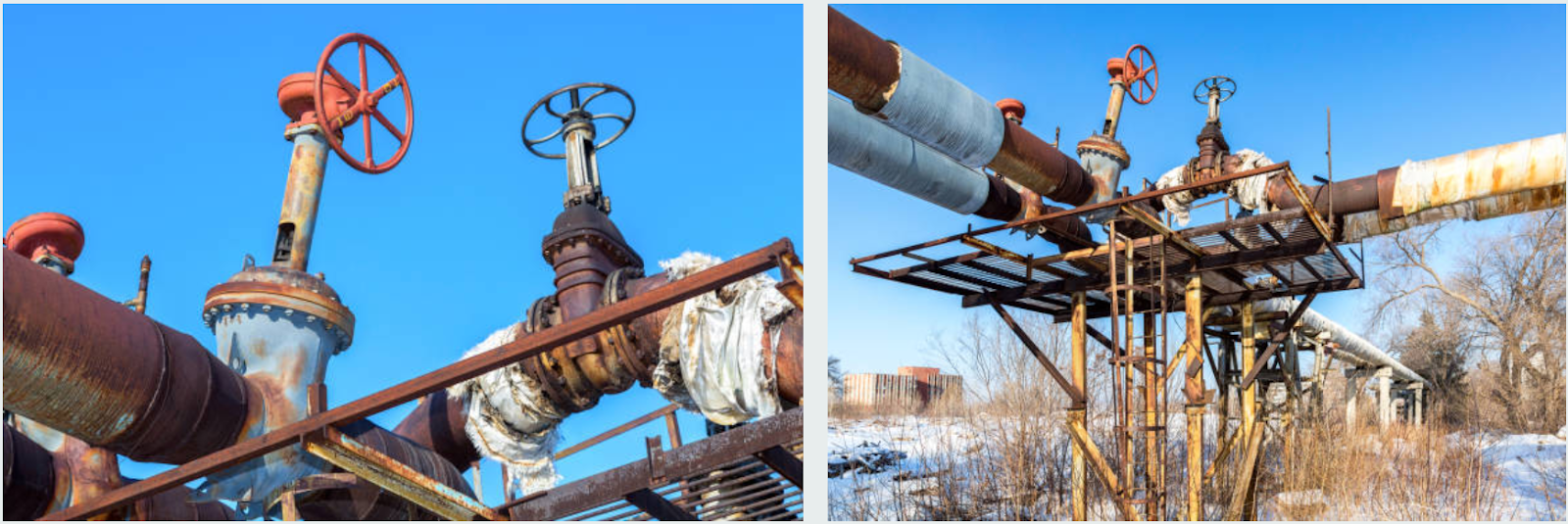
Preventative Measures for Corrosion
Preventative measures can be taken to reduce the risk of corrosion. One of the most effective ways to prevent corrosion is to use corrosion-resistant materials, such as stainless steel or aluminum. These materials are less likely to corrode and can provide long-term protection against corrosion.
Another important preventative measure is to properly maintain and clean equipment and surfaces. Regular cleaning and inspections can identify potential corrosion issues early on and prevent them from becoming more serious problems. Properly maintaining equipment and surfaces also includes protecting them from exposure to harsh environments and chemicals.
Coating and painting surfaces with corrosion-resistant materials is another effective preventative measure. These coatings and paints provide a barrier between the metal surface and the environment, protecting the metal from corrosive agents. However, it's important to note that these coatings and paints will eventually degrade and need to be reapplied to maintain their effectiveness.
Lastly, it's also important to implement corrosion monitoring systems that can detect corrosion at an early stage. This allows for timely maintenance and repairs, which can greatly reduce the impact of corrosion on equipment and production.
Conclusion
Corrosion is a major problem in the energy industry, causing high costs in the form of maintenance, equipment downtime, asset replacement, and lost production. Understanding the root causes and appropriate mitigating strategies for corrosion is essential for effectively combatting this costly problem. By taking the time to understand and address the underlying issues, implementing preventative measures and monitoring systems, we can reduce the impact of corrosion on equipment, production, and overall industry costs.
0 Comments