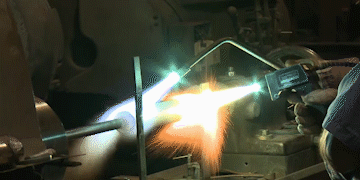
What is Thermal Spray Coating?
Thermal Spray Coating is a surface engineering process in which a material is melted and sprayed onto a surface to form a coating. The process is used to improve the surface properties of a material, such as its wear resistance, corrosion resistance, and thermal insulation.
Thermal Spray Coating Processes
There are all different types of thermal spray coating processes used in various industrial applications for surface treatment and modification. Each method offers unique advantages and is used depending on the specific requirements of the application, including:
- HVOF (High-Velocity Oxygen Fuel) spraying
- Plasma spraying
- Arc spraying
- Flame spraying
- Cold spraying
HVOF (High-Velocity Oxygen Fuel) spraying: HVOF is a process that involves the combustion of gases such as hydrogen, acetylene, or propane with oxygen in a combustion chamber. The hot gases and molten particles are then accelerated through a nozzle at high velocities and sprayed onto the surface to be coated. HVOF spraying is known for producing coatings with high-density, low porosity, and high bond strength, making it suitable for wear and corrosion-resistant coatings.
Plasma spraying: In plasma spraying, a plasma arc is created between a cathode and an anode, and a gas is introduced into the arc, which is ionized to form a plasma. The plasma is then used to melt the coating material, which is then propelled onto the surface to be coated. Plasma spraying is known for its ability to produce coatings with a very high degree of purity and controlled porosity. It is used for high-temperature coatings, thermal barrier coatings, and bioactive coatings, among others.
Arc spraying: Arc spraying is a process that uses an electric arc to melt the coating material, which is then sprayed onto the surface. The process involves passing an electric current through two consumable wires, which creates an arc between them, and the heat generated melts the wire, which is then sprayed onto the surface. This process is known for its high deposition rate and is used for coatings that require thickness, such as corrosion protection.
Flame spraying: Flame spraying uses the heat generated by burning fuel gases such as propane, acetylene, or hydrogen to melt the coating material, which is then sprayed onto the surface to be coated. This process is relatively simple and can be used for a wide range of materials. Flame spraying is known for producing coatings with high bond strength and is commonly used for coatings that require a high degree of adhesion.
Cold spraying: Cold spraying is a process that uses high-pressure gas to accelerate fine metal or ceramic particles at supersonic speeds, which creates a cold spray that melts and forms a coating on the surface. Unlike other thermal spray coating methods, the process does not rely on heat to create the coating, making it suitable for temperature-sensitive materials. Cold spraying is known for producing coatings with high density, low porosity, and excellent bonding strength.
How to Prepare a Surface for Thermal Spray Coating
Before applying a thermal spray coating, it is important to prepare the surface properly. The surface should be clean and free of any contaminants, such as oil, grease, or rust. The surface should also be roughened or textured to provide a good mechanical bond between the coating and the substrate.
The preparation process may involve several steps, such as:
- Cleaning the surface with a solvent or detergent
- Blasting the surface with abrasive particles
- Applying a bond coat to improve the adhesion of the thermal spray coating
In summary, these thermal spray coating methods offer a wide range of options for surface modification and treatment in industrial applications. Depending on the requirements of the application, one or more of these methods may be suitable for producing coatings with specific characteristics such as hardness, wear resistance, and corrosion protection.
0 Comments