
A Basic Guide to Pipe Coating: Asphalt Enamel, Fusion Bonded Epoxy, 3 Layer Polyethylene, and 3 Layer Polypropylene
Pipe coating is an essential step in protecting and prolonging the lifespan of pipelines, whether they are used for water and sewage systems, oil and gas transportation, or other industrial applications. There are a variety of coating options available, each with their own unique benefits and drawbacks.
Asphalt Enamel
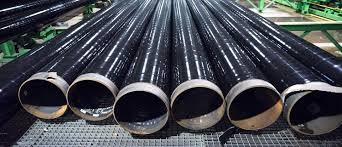
Asphalt enamel, also known as coal tar enamel, is a popular choice for pipe coating due to its durability and resistance to corrosion. This coating is typically applied by spraying or brushing onto the surface of the pipe, and it dries to form a hard, protective layer. Asphalt enamel can withstand high temperatures and is resistant to chemicals, making it a good choice for pipelines that transport hot liquids or are exposed to harsh environments.
Fusion Bonded Epoxy
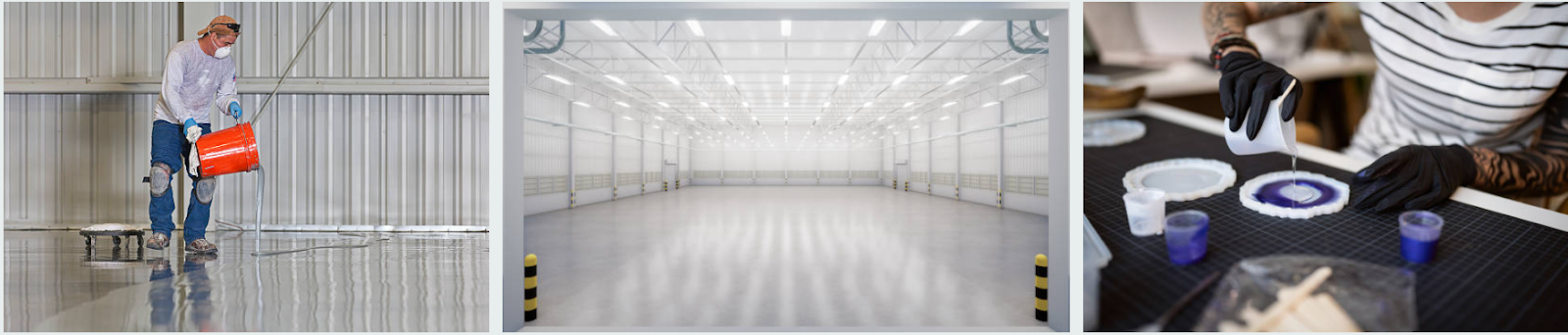
Fusion bonded epoxy (FBE) is another commonly used pipe coating option. This coating is applied as a dry powder, which is then heated to form a hard, protective layer on the surface of the pipe. FBE is highly resistant to corrosion and abrasion, making it a good choice for pipelines that will be buried underground or exposed to harsh environments. Additionally, FBE can be applied to both steel and concrete pipes.
3 Layer Polyethylene
3 Layer Polyethylene (3LPE) is a multi-layer coating system that provides excellent corrosion protection for steel pipelines. The coating is made up of three layers: a layer of epoxy primer, a layer of adhesive, and a layer of polyethylene. This coating can be applied by extrusion or spraying, providing a tough and durable barrier to protect the pipe from external influences like soil and water. 3LPE is often used in buried pipelines, as well as pipelines that transport oil, gas, and chemicals.
3 Layer Polypropylene
3 Layer Polypropylene (3LPP) is similar to 3LPE, but it is made up of three layers of polypropylene. This coating is also highly resistant to corrosion and abrasion, and it is often used in pipelines that transport oil, gas, and chemicals. 3LPP is also commonly used in buried pipelines, as well as pipelines that are exposed to harsh environments.
You might be interested in :
Conclusion
In conclusion, the type of pipe coating you choose will depend on the specific needs of your pipeline, including the type of fluid it will be transporting, the environment it will be exposed to, and the level of corrosion protection required. Asphalt enamel, Fusion Bonded Epoxy, 3 Layer Polyethylene, and 3 Layer Polypropylene are some of the most popular coating options available, each with their own unique benefits and drawbacks.
0 Comments