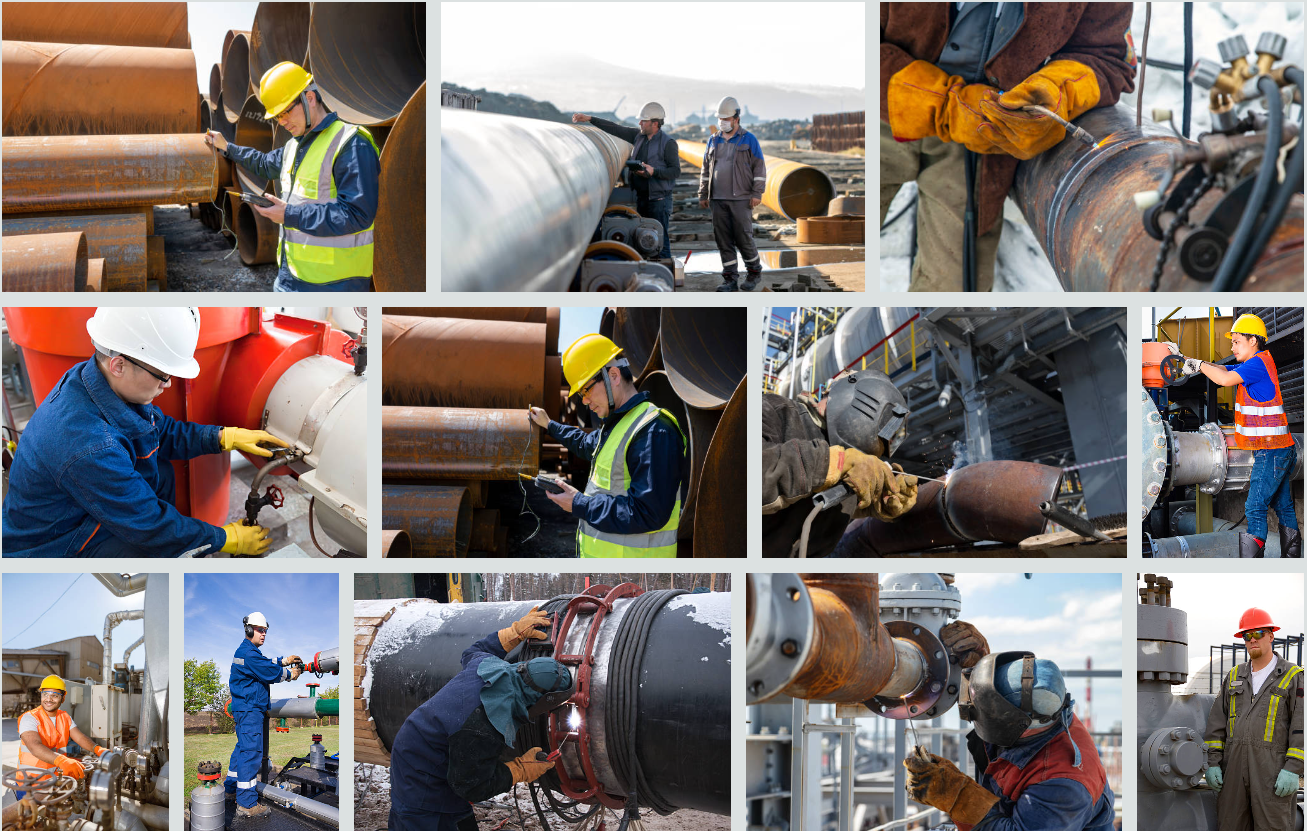
Mechanical Construction of Piping Site Installation in Mechanical Construction for Offshore Oil and Gas Projects
Installing piping systems on construction sites requires a great deal of precision and attention to detail to ensure that the finished product is safe and functional. This blog post will discuss the various steps involved in the mechanical construction of piping site installation, including material receiving inspection, fit up, purging gas control, welding monitoring, and more.
1. Material Receiving Inspection
Before any construction can begin, all materials must be thoroughly inspected to ensure that they meet the required specifications. This includes checking for any damages or defects, and verifying that the materials are the correct type and size for the project.
2. Fit Up (for Duplex & Superduplex)
Once materials have been received and inspected, the next step is to begin fitting them together. This is a crucial step, as it ensures that all pieces are properly aligned and that there are no gaps or misalignments that could cause problems later on.
3. Purging Gas Control (for Duplex & Superduplex)
Purging gas control is an important part of the welding process, as it helps to remove any contaminants or gases that could negatively impact the quality of the welds. This step is particularly important when working with duplex and superduplex materials, which are more prone to corrosion and require extra care during welding.
4. Welding Electrical Parameters Monitoring (for Duplex & Superduplex)
To ensure that the welding process is performed correctly and that the finished product is of the highest quality, it is important to monitor a variety of electrical parameters throughout the process. This includes monitoring the voltage, current, and wire feed speed to ensure that they are within the proper range for the specific materials being used.

5. Welding Interpass Temperature Monitoring (for Duplex & Superduplex)
In addition to monitoring electrical parameters, it is also important to monitor the interpass temperature during welding. This helps to ensure that the material is not overheating, which can cause warping or cracking.
6. Welding Monitoring (for Duplex & Superduplex)
Welding monitoring is an ongoing process that involves carefully observing the welding process to ensure that everything is proceeding as planned. This includes checking for proper penetration, ensuring that the welds are the correct size and shape, and looking for any signs of defects or problems.
7. Welding Visual Inspection
Once the welding is complete, a visual inspection must be performed to ensure that all welds are of the highest quality. This includes checking for proper penetration, ensuring that the welds are the correct size and shape, and looking for any signs of defects or problems.
8. Orifice Flanges (Root Penetration Visual Check)
Orifice flanges are an important part of piping systems, and it is crucial to ensure that they are properly installed and functioning. One important step in this process is to perform a visual check of the root penetration, which helps to ensure that the flanges are properly sealed and that there are no leaks.
9. Reinforcement Pad Welding
Reinforcement pad welding is the process of adding additional material to certain areas of the piping system to increase its strength and durability. This is typically done in areas that will be subjected to high levels of stress or pressure, such as at the base of a pipe support.
10. Reinforcement Pad Testing (Test only for UOP License Lines)
After reinforcement pad welding is complete, it is important to perform testing to ensure that the added material is providing the desired level of support and strength. This testing is typically done on UOP license lines, which are subject to specific regulations and requirements.
11. Welding Repair and NDE (if applicable)
If any issues or defects are identified during the inspection process, welding repairs may be necessary. Non-destructive examination (NDE) techniques such as radiography or ultrasonic testing may also be performed to ensure that the repair has been done correctly and that the piping system is safe and functional.

12. Piping Alignment, Leveling and Dimensional Control
After all welding and repairs have been completed, the next step is to ensure that the piping system is properly aligned and level. This includes checking that all pipes and fittings are in the correct position and that they are the correct size and shape.
13. Flanged Joints Parallelism
Flanged joints are an important part of piping systems and it is crucial to ensure that they are properly aligned and parallel. This helps to ensure that the system is leak-free and that the flanges are able to properly seal.
14. Flanged Joints Tightened
Once the flanged joints have been aligned, they must be tightened to the correct torque. This ensures that the flanges are properly sealed and that there are no leaks in the system.
15. Pressure Test
To ensure that the piping system is safe and functional, a pressure test must be performed. This involves filling the system with water or air and increasing the pressure to a specified level. Any leaks or defects will become apparent during this test.
16. Draining and Air Blowing for Drying
After the pressure test is complete, the piping system must be drained and dried. This is typically done by blowing air through the system to remove any remaining water or moisture.
17. Spring Supports Cold Regulation
Spring supports are used to provide additional support and stability to the piping system. During the installation process, it is important to adjust the spring supports to the correct tension, or 'cold regulation' to ensure that they are providing the proper level of support.
18. Reinstatement
Reinstatement is the process of returning the construction site to its original condition. This includes cleaning up any debris, restoring any areas that were disturbed during the installation process, and ensuring that the site is safe and ready for use.
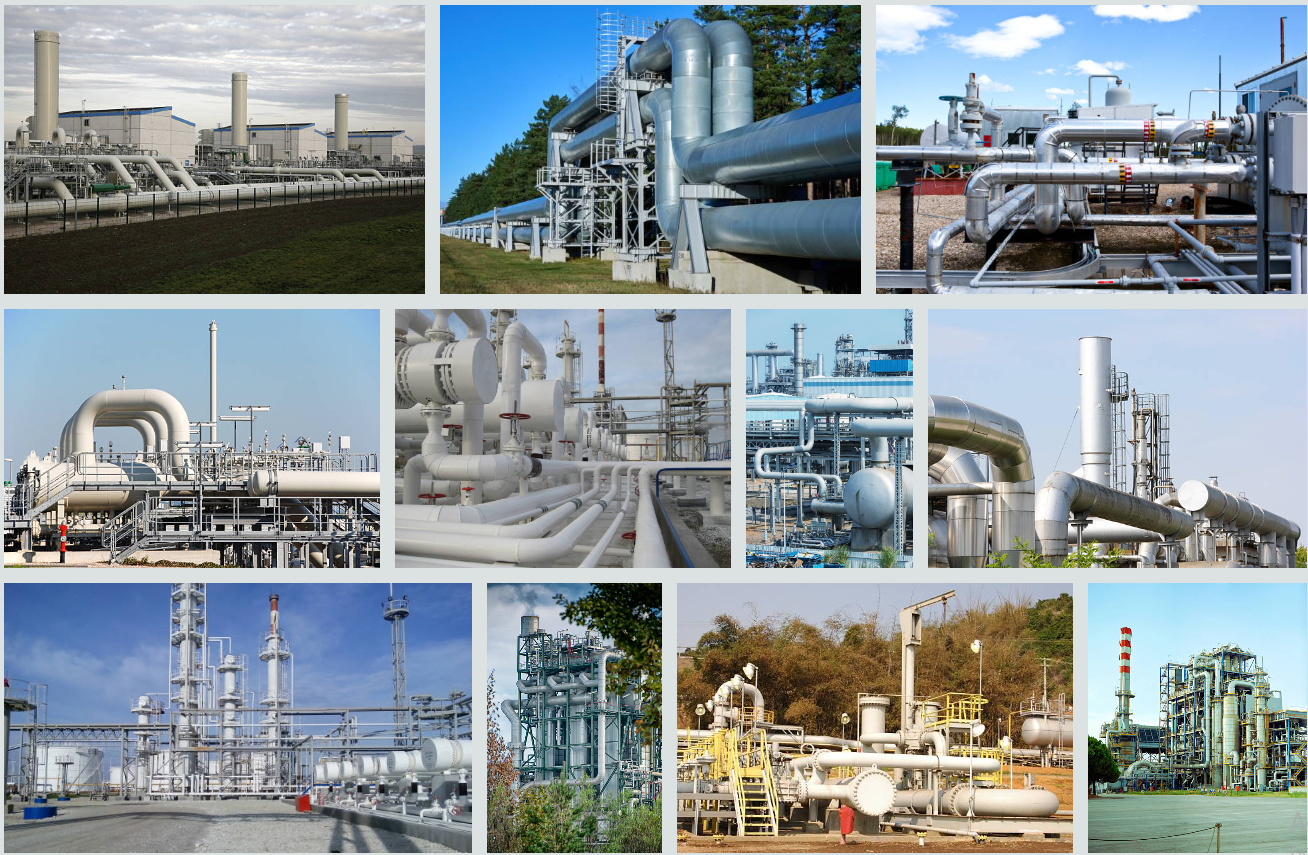
19. Final Acceptance
Once all of the above steps have been completed, the piping system will be inspected one final time to ensure that it is safe and functional. If it passes inspection, it will be accepted and put into operation, and the construction project will be considered complete. This final acceptance process is critical to ensure that the piping system meets all relevant regulations, codes and standards and is safe for operation. Overall, the mechanical construction of piping site installation is a complex process that requires a great deal of skill and attention to detail to ensure that the finished product is safe and functional.
0 Comments